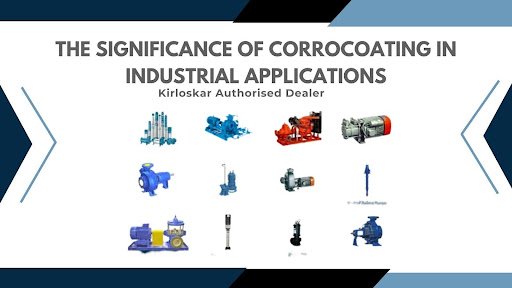
Corrosion is one of the most problematic issues with industrial equipment like pumps, valves, pipes and tanks. But corrocoating is one technique that can help you combat it effectively. Corrocoating has significant use in chemical and wastewater treatment plants as corrosion can drastically reduce the working life of equipment as they are exposed to moisture. VEMC is one of the leading industrial water pump suppliers in Mumbai, and in collaboration with Kirloskar Corrocoat, undertakes turnkey projects for coating a wide range of electromechanical equipment.
Types of corrosion
Here are the main types of corrosion found in electromechanical equipment.
- Uniform corrosion: This type of corrosion occurs over the entire surface of a metal. Although it is one of the most benign forms, nevertheless it requires prevention as well.
- Pitting corrosion: Being hard to predict, detect and characterise, this type of corrosion can be highly destructive. As the name suggests, it leads to the formation of vertical holes or cavities on the surface of a metal. This type of corrosion can be caused due to local break or damage in protective coating. It can cause sudden failure of equipment despite relatively low loss of metal.
- Crevice corrosion: It is also a localised form of corrosion usually resulting from stagnant microenvironment with a difference in concentration of ions between two areas of a metal. It affects shielded areas like under washers, gaskets, bolt heads , etc., with limited oxygen supply.
- Inter-granular corrosion: It is caused by impurities present at the grain boundaries and occurs along or adjacent to these grains. While the bulk of the metal remains intact, it affects its mechanical properties.
- Galvanic corrosion: It is the degradation of metals near the joint which occurs when two electrochemically different metals are in contact in an electrolytic environment.
Benefits of corrocoating
- Increased lifespan: With corrocoating, users can expect a longer lifespan for their electromechanical equipment which reduces the need to replace or repair them frequently. This also reduces the waste that entails due to replacement of old equipment and is hence in line with the concept of circular economy.
- Cost savings: By avoiding frequent breakdowns due to corrosion, users can save significant amounts of repair and maintenance costs.
- Reduced downtime: Corrosion can impact some of the most critical pieces of equipment in your business facility leading to sudden and unforeseen downtime. This can be successfully avoided with protective corrocoating.
Case in point: MCGM Complex Pump Corrocoating Project
VEMC has undertaken a number of large-scale corrocoating projects in the past. In 2015, we corrocoated the crucial Municipal Corporation of Greater Mumbai (MCGM) Complex Pump at Bhandup. The pump was affected by heavy pitting corrosion inside the casings. It was taken to KBLs Hydraulic Research Centre where it was blasted, coated and inspected. The corrocoating didn’t just ensure the protection of the pump from corrosion but also showed instant results in terms of better efficiency, input power and head.